A Taylor Company Certified Red Seal Technician in Canada follows a systematic approach when working on a Taylor 349 commercial slush machine. This ensures that the machine is installed, maintained, and repaired according to the highest standards. The Taylor 349 is a popular commercial slush machine, often found in convenience stores like 7-Eleven or Circle K, and other establishments that serve frozen beverages. Here’s an overview of what the technician’s job entails:
Installation
- Pre-Installation Planning: This involves ensuring the site is ready for the machine, including adequate space, power supply, and ventilation. The technician reviews the installation site to ensure it meets the requirements for the Taylor 349 machine.
- Unpacking and Inspection: The machine is carefully unpacked and inspected for any damage that might have occurred during shipping. All parts are accounted for, including any accessories and manuals.
- Setting Up: The technician assembles and sets up the machine according to the Taylor Company’s specifications. This includes connecting it to the power supply and water line (if applicable), ensuring its level, and verifying that all components are securely in place.
- Initial Testing: Before the machine is handed over for use, it undergoes initial testing to ensure it operates correctly. This includes running the machine through a few cycles to ensure the freezing mechanism and dispensers work as expected.
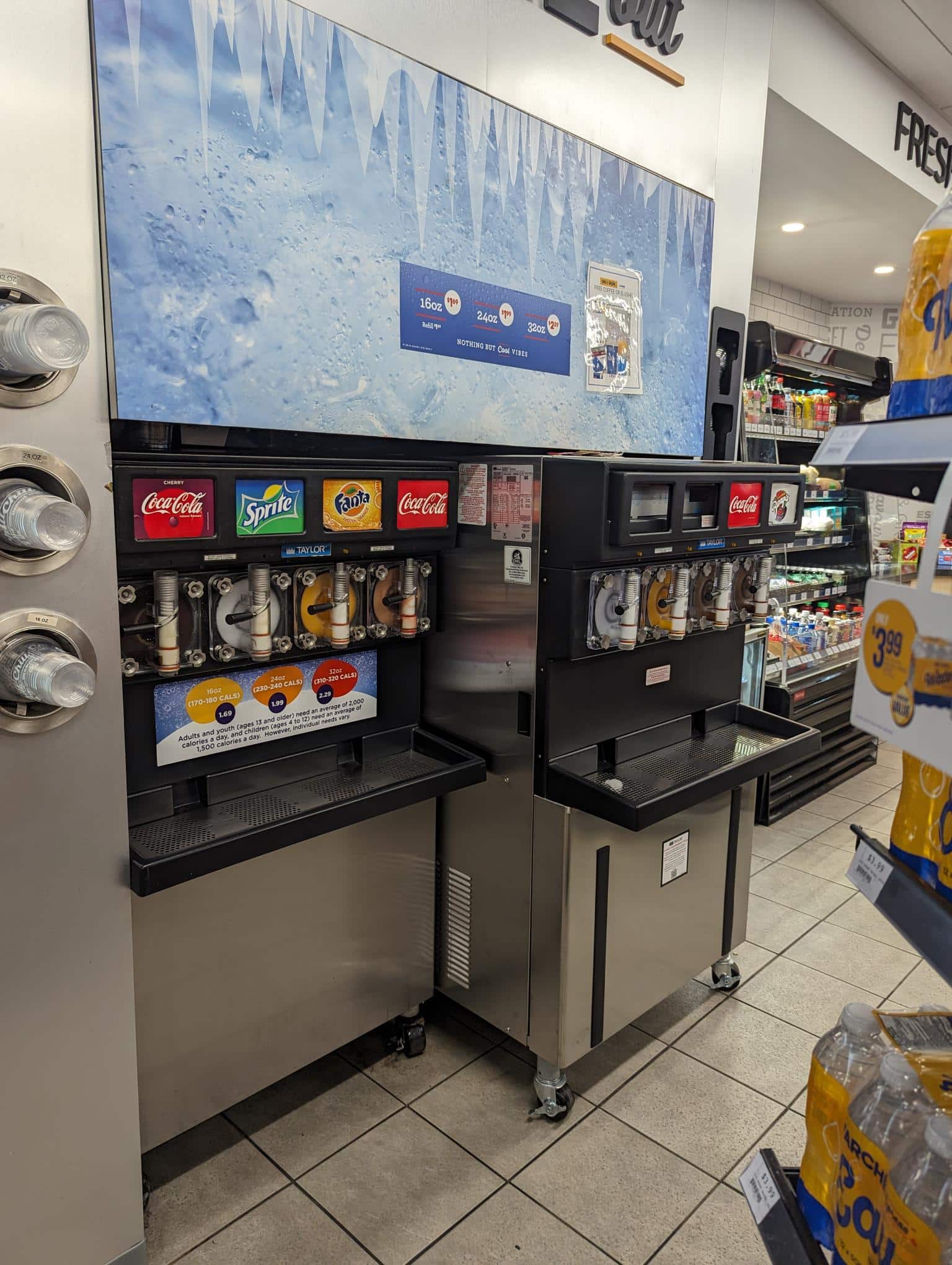
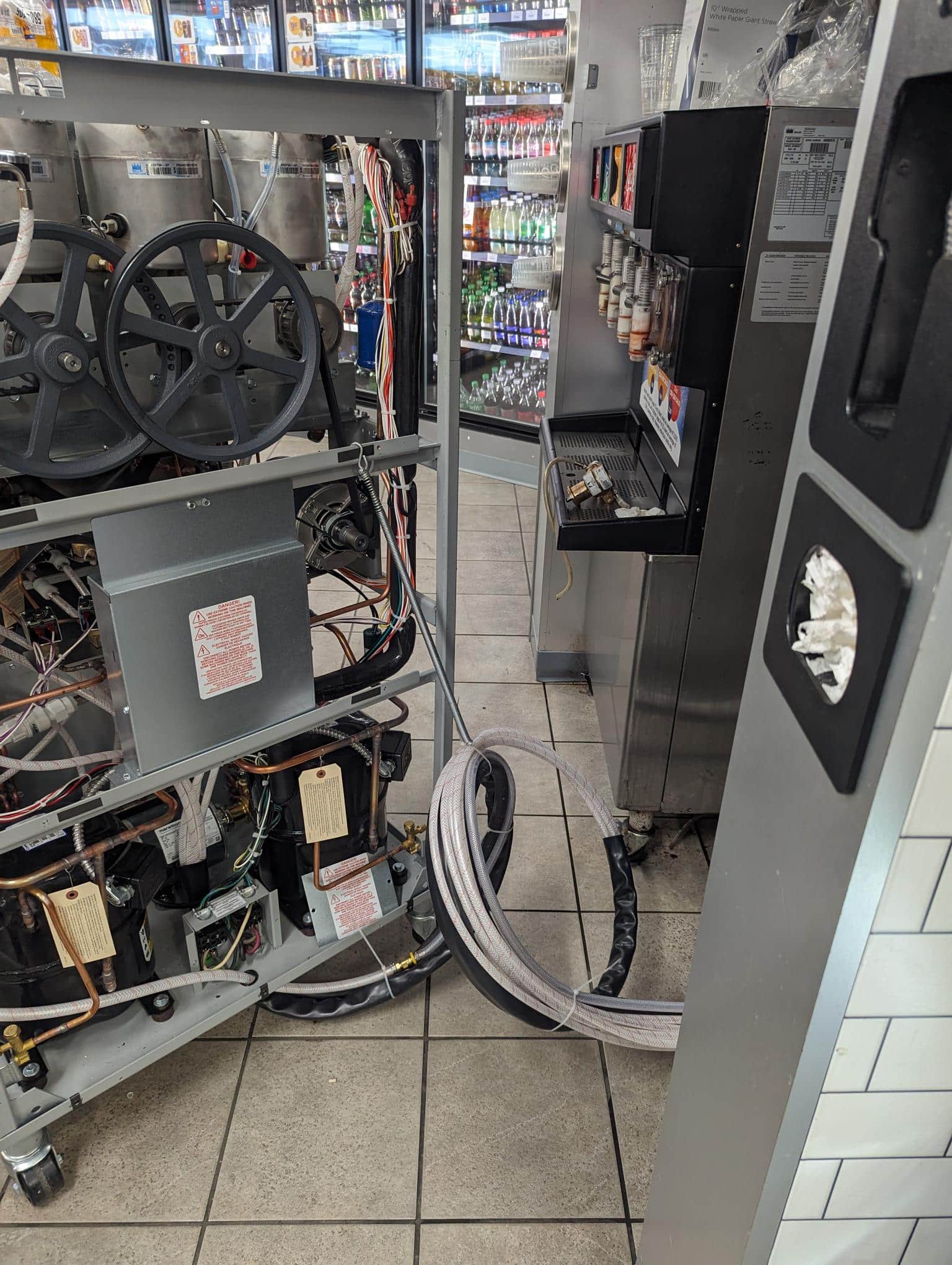

Maintenance and Repair
- Routine Maintenance: The Red Seal Technician performs routine maintenance checks to prevent issues from arising. This includes cleaning the machine, checking and replacing seals and filters, and ensuring the refrigeration system is functioning correctly.
- Troubleshooting: If a problem arises, the technician uses their expertise to diagnose the issue. This could involve electrical testing, checking the refrigeration system, or inspecting mechanical components for wear and tear.
- Repairs: Once the problem is identified, the technician carries out the necessary repairs. This could involve replacing faulty parts, repairing electrical issues, or fixing refrigeration components. They use only Taylor-certified parts to ensure compatibility and reliability.
- Safety and Compliance: Throughout the installation and repair processes, the technician adheres to safety standards and regulations. In Canada, this means following the guidelines set out by provincial and federal safety regulations, as well as industry best practices.
- Customer Education: After installation or repair, the technician often educates the customer on proper machine operation, cleaning procedures, and basic troubleshooting. This empowers the machine’s operators to maintain optimal function and minimize downtime.
- Documentation: The technician documents all installation and repair activities, providing a clear record of the work performed. This documentation is crucial for warranty purposes and future maintenance needs.
Certification and Skills
- A Red Seal endorsement in Canada signifies that a technician has achieved a high standard of expertise in their trade. While the Red Seal program covers a range of trades, technicians working on specialized equipment like Taylor machines undergo specific training provided by the manufacturer or through specialized courses.
- These technicians possess a deep understanding of mechanical, electrical, and refrigeration systems, enabling them to install and repair complex machinery like the Taylor 349 slush machine.
By adhering to these procedures, Taylor Company Certified Red Seal Technicians ensure that Taylor 349 slush machines are installed and maintained to perform reliably, ensuring businesses can serve their customers without interruption.
Reach out today!
Interested in learning more about slush equipment? Contact us today to schedule a service visit or learn how DSL can support your business. You can contact us through our dedicated service hotline at 1-800-665-1125, text via 1-780-452-7580, email at service@dslinc.com, or through our website’s contact form.