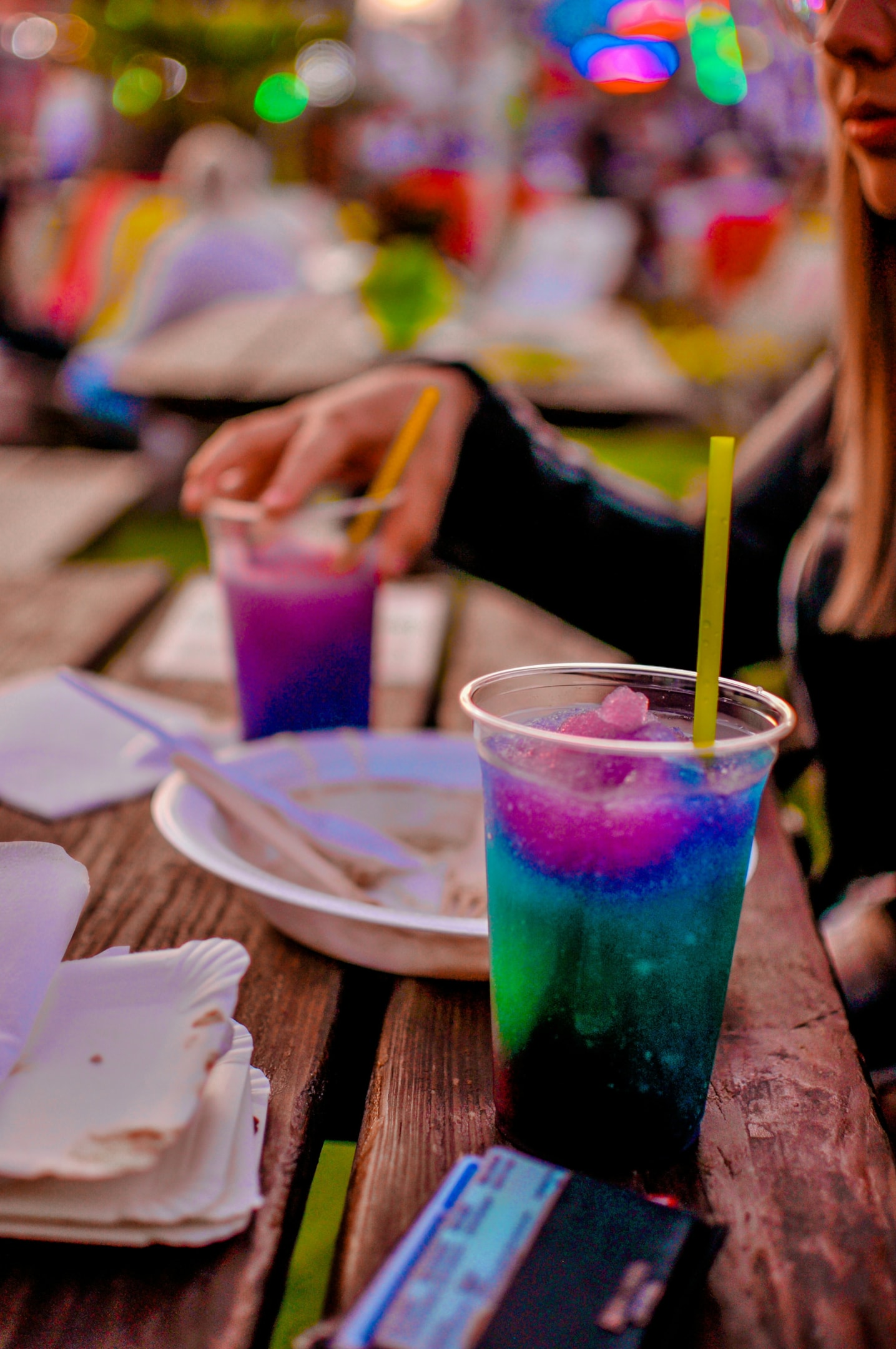
Are you experiencing issues with your slush machine? This slush machine troubleshooting guide is designed to help you fix the most common problems quickly. We’ll address non-freezing slush, mixture inconsistencies, and noise issues and provide actionable steps for each. Read on for a clear and direct solution to get your slush machine back in perfect working order.
Key Takeaways
- Regular maintenance, including cleaning and lubrication, is crucial to prevent common slush machine issues such as non-freezing and inconsistent mixtures.
- Monitoring and adjusting syrup-to-water ratios, alongside checking temperature settings, can address slush consistency and freezing problems effectively.
- Persistent mechanical noises or leaks indicate the need for professional evaluation, while preventive measures like using night mode and maintaining seal integrity help avoid future issues.
Identifying Common Slush Machine Issues
Recognizing common slush machine issues is the first step in slush machine troubleshooting and maintaining your equipment. Among the most frequent problems are non-freezing, inconsistencies in the slush mixture, and unwanted noise during operation. These issues can stem from regular maintenance lapses.
Understanding these issues and their causes is vital. For instance, a machine not freezing might be due to incorrect temperature settings or a faulty micro-switch. Mixture inconsistencies could result from an incorrect slush ratio or thick syrup mixtures, and unwanted noise often indicates mechanical issues. Awareness of these problems allows for proactive steps to ensure smooth operations and customer satisfaction.
Troubleshooting a Non-Freezing Slush Machine
Understanding slush machine troubleshooting is essential for every operator to ensure optimal performance and longevity of the equipment.
One of the most frustrating issues you might encounter is a slush machine that refuses to freeze. This issue can stem from incorrect power supply or temperature settings. Faulty micro-switches, stuck valve stems, or issues with the thickness setting screw are other potential causes.
A systematic approach is necessary to address a non-freezing slush machine. Begin by checking the temperature settings, then inspect the condenser and verify the syrup ratios. These steps help pinpoint the cause and restore optimal freezing.
Checking Temperature Settings
Proper temperature settings are crucial for achieving the perfect slush consistency. A temperature between -2 and -3 degrees Celsius is ideal for commercial slush machines. Verify that the machine is plugged in and receiving power, as a lack of power can hinder freezing.
Correct temperature settings are essential. Adjust settings as needed for the desired consistency. This step often resolves freezing issues, ensuring optimal frozen drinks.
Inspecting the Condenser
The condenser is crucial to the slush machine’s cooling system. Regular cleaning maintains condenser efficiency and effective machine operation. A dirty condenser can impede proper freezing.
Regular maintenance checks and cleaning keep the condenser in good shape. This sustains cooling performance and prevents issues that could disrupt operations.
Verifying Syrup Ratios
The syrup-to-water ratio is crucial in preventing freezing issues. A 6:1 ratio helps avoid overly thick mixtures that won’t freeze properly. A refractometer can measure sugar content, ensuring a Brix reading between 13 and 15 degrees.
Monitoring syrup ratios and sugar content prevents the slush from failing to freeze or becoming too solid. This practice maintains the desired texture and consistency of your frozen drinks.
Addressing Slush Mixture Inconsistencies
Inconsistent slush mixtures can significantly impact the quality of your frozen drinks. Adjusting the water-to-syrup ratio (typically 1:4 or 1:5) tailors the slush mixture’s consistency. Proper temperature and consistency are crucial for correct freezing.
Insufficient sugar can lead to large ice blocks, affecting the quality of slush syrup. Thick syrup mixtures can also cause excessive freezing or ice block formation.
Consistent slush mixtures ensure optimal dispensing and texture, leading to customer satisfaction with quality slush syrup.
Resolving Unwanted Noise in Slush Machines
Unwanted noise often indicates underlying issues in a slush machine. Persistent grinding or squealing usually indicates gear motor problems at the machine’s back. Identify noise sources by listening for changes when turning off each spiral’s rotation.
Clicking or knocking sounds may be expected in new machines as motors settle but should diminish over time. Persistent noise may indicate a mechanical issue requiring professional evaluation and repair.
Fixing Leaks and Seal Problems
Leaks, often caused by damaged seals and gaskets, can be significant issues in a slush machine. First, you need to identify the source of the leak. Tap leaks can often be resolved by lubricating the tap mechanism or replacing damaged seals.
Slush-colored liquid leaking from the overflow outlet indicates internal damage. Check the seal and shaft for wear. Replacing a worn seal is straightforward, but a damaged shaft may require professional assistance.
Maintaining Your Slush Machine for Optimal Performance
Regular maintenance keeps your slush machine running smoothly and prolongs its lifespan. Proper care prevents damage and ensures efficient operation. Regular cleaning protects your investment, maintains health standards, and ensures customer satisfaction.
Weekly cleaning, including washing parts and lubricating seals, is essential for longevity and performance. Removing dust from the condenser grill improves airflow and freezing efficiency. A 15cm clearance around the slush machine facilitates proper airflow for efficient freezing.
Regular Cleaning Procedures
Weekly cleaning and lubrication are essential to extending the slush machine’s lifespan. Cleaning involves draining the slush, washing with lukewarm, soapy water, and thorough rinsing to remove residues. Warm water with mild detergent ensures effective sanitization and the regular slush machine maintenance is crucial for optimal performance.
For proper lubrication, use food-safe petroleum grease on O-rings and seals. Lubricate the sizeable round seal at the back and the soft seal on the drive shaft.
Regular proper maintenance extends the machine’s lifespan and ensures smooth operation.
Lubrication Tips
Proper lubrication minimizes friction, enhances performance, and prolongs the machine’s life. Lubricated parts operate smoothly, reducing noise and increasing efficiency. Food-safe petroleum grease is essential for this task.
Reduced wear on components results in lower maintenance costs and fewer breakdowns. Regularly lubricate the motor gearbox and moving parts to keep the machine in excellent condition.
When to Contact a Professional
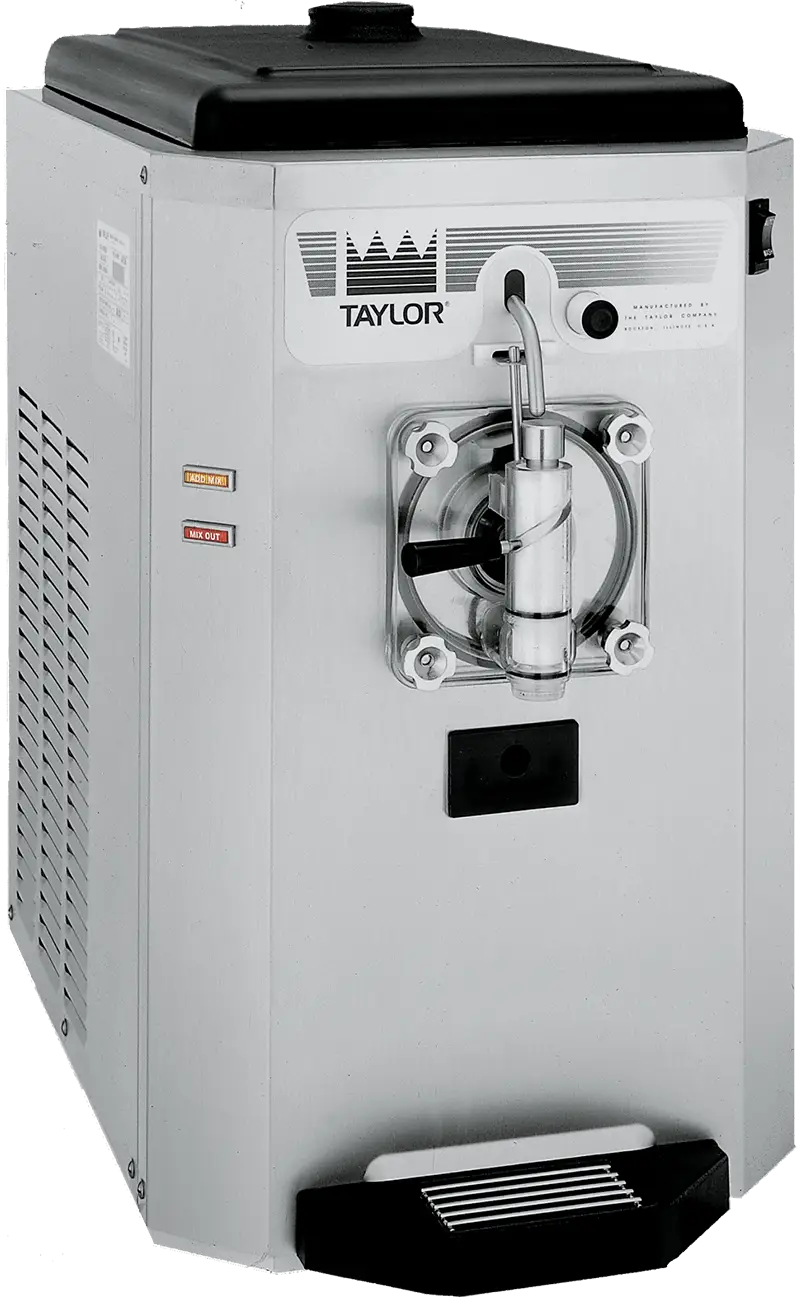
Some situations require professional intervention despite regular maintenance and troubleshooting tips. If maintenance tips fail, contact a professional. Electrical malfunctions or consistent overheating indicate the need for expert help.
Frequent ice accumulation may indicate serious problems needing expert attention. Timely professional assistance prevents further damage and ensures safe, efficient operation.
Quality of the Slush Machine
The quality of the machine also plays a massive factor in how your slush machine performs, lasts, and is maintained. A high-quality commercial slush machine will make and save you more money in the long run. An excellent routine system is often more efficient and better with expert help.
Preventive Measures to Avoid Future Issues
Preventive maintenance avoids future issues. Perform thorough cleaning weekly or after every 500 drinks, focusing on sanitizing and checking seals. Keeping slush tanks at least half full prevents over-freezing and damage to the dispensing handle.
Switching to night mode at closing avoids ice buildup and protects the machine’s components. Rubber seals should be replaced annually as they deteriorate, while plastic components typically last the machine’s lifetime.
These preventive measures ensure the longevity and optimal performance of your slush machine.
Summary
Maintaining your slush machine through regular cleaning, proper lubrication, and timely troubleshooting is essential for providing the best-frozen drinks and ensuring customer satisfaction. Addressing common issues like non-freezing, mixture inconsistencies, and unwanted noise can prevent more serious problems. Contact the professionals if you have any questions.
Following this guide can keep your slush machine running smoothly and efficiently. Remember, a well-maintained machine enhances the quality of your frozen drinks and boosts customer satisfaction and sales. Stay proactive with your slush machine maintenance.
Frequently Asked Questions
What should I do if my slush machine is not freezing?
If your slush machine is not freezing, check the temperature settings and confirm that the machine is receiving power. Additionally, inspect the condenser and verify the syrup ratios to ensure proper operation.
How often should I clean my slush machine?
You should clean your slush machine regularly every week and thoroughly after every 500 drinks served or bi-weekly.
What is the ideal syrup-to-water ratio for slush mixtures?
For optimal consistency and to avoid freezing issues in slush mixtures, the ideal syrup-to-water ratio is 6:1.
How can I resolve unwanted noise from my slush machine?
To resolve unwanted noise from your slush machine, identify the source. Listen for changes when turning off the rotation of each spiral and check the gear motor for any issues. Addressing these specific components often effectively eliminates the noise.
When should I contact a professional for slush machine issues?
If basic maintenance does not resolve the problem with your slush machine, particularly electrical malfunctions or persistent overheating, you should contact a professional. Seeking expert assistance can prevent damage and ensure safe operation.